Making Safety the Priority at Potters
Due to the nature of their manufacturing process, Potters knows that safety must be a top priority for every employee, regardless of their role. To accomplish this, Potters built a unique strategy for managing safety at its plants. Across the 31 manufacturing facilities around the world, Potters applies and upholds OSHA safety standards regardless of whether those standards exceed local regulation. In addition, Potters’ approach to safety metrics and building a culture of safety are distinct.
Safety Metrics
In addition to OSHA-standard safety KPIs, Potters developed proprietary metrics to ensure they have a holistic view of HSE performance. For example, Potters created the Preventative Ratio which considers leading indicators, such as near miss safety events, hazard observations, and risk assessments, alongside lagging indicators, including incidents and environmental spills. Potters also tracks Perfect Days, or days without safety incident. The goal of this metric is to encourage every employee to start each day with the goal of making it perfect, without focusing on what happened in the past or what might be coming up tomorrow.
Potters also takes a differentiated approach to metrics like DART (days away, restricted, or transferred). Rather than focusing on the injuries that lose time versus the injuries that do not lose time, Potters treats every reportable with the same level of care. Every reportable injury requires investigations and corrective plans, regardless of severity.
CEO Leadership and Safety Culture
Accountability for safety starts at the top, with the Potters CEO leading safety across the company. Any time there is a recordable injury anywhere in the world, the CEO leads the incident review meeting regardless of the severity of the incident. Each year, Potters also issues the “CEO Safety Recognition Award” and the CEO’s “Most Improved Award” to those plants that have exhibited strong safety performance over time. Other members of the leadership team are also expected to take accountability for safety. For example, each member of the leadership team is assigned as ambassador to several plants and conducts an in-depth safety review during their visits, among other responsibilities.
Potters built a safety culture where accountability extends to all levels of the organization. They use tools such as their Stop Work Authority card, which gives individuals authority to stop, act, or stop an unsafe behavior or condition. This is an important tool to empower any employee at Potters to risk-assess a situation, act, and repeat, and build trust that there will be no consequence for stopping work if they believe conditions are unsafe.
It should not be assumed that the investment above was or will be profitable. Please see “LEGAL” page for important information regarding this content.
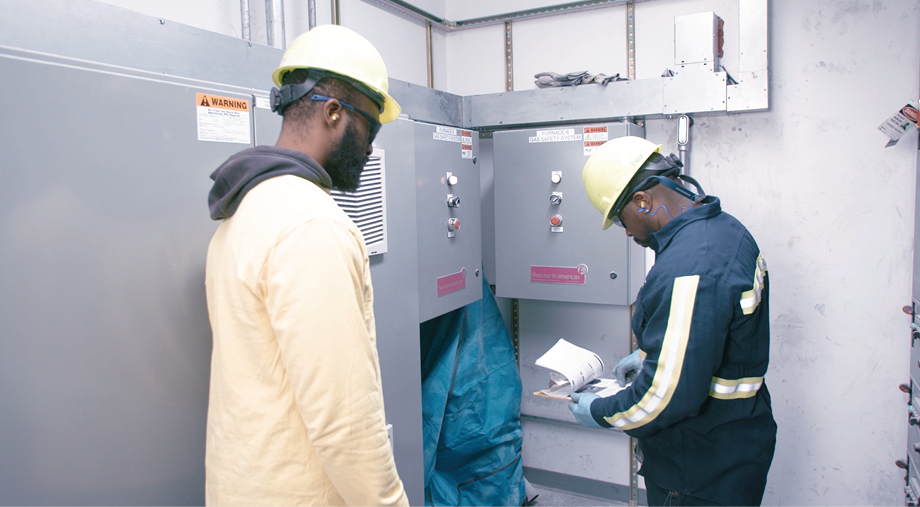
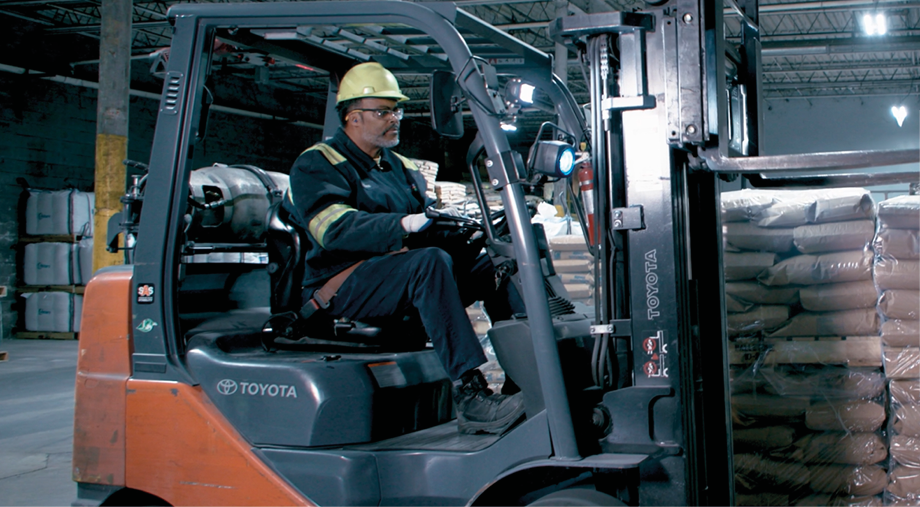